Sandeep Nijhawan introduced 4 enterprise concepts, every addressing rising international temperatures, to his March 2020 assembly with an investor at Bill Gates-founded Breakthrough Energy Ventures. Freshly departed from founding two startups — one on hydrogen, one other on batteries — Nijhawan had simply seven slides to present. The first pitch in his deck was to make iron with out coal, intense warmth or emissions, powered by solely renewable electrical energy.
“Let me stop you right there,” BEV investor Dave Danielson advised him. “If you could do this thing, then that’s what I would do. I don’t want to hear the next three ideas.”
Iron, after all, makes up 98% of the substance in metal, the ever present materials that’s constructed the fashionable world. In furnaces heated by coal to greater than 1400°C (2500°F), the carbon in coal combines with the oxygen in iron ore to separate out impurities and undesirable oxygen atoms, releasing enormous quantities of carbon dioxide.
The iron later goes by way of a collection of steps to be became metal, however the iron-creation step accounts for 90% of the greenhouse gasoline generated. Steel manufacturing is accountable for 7% of greenhouse-gas emissions dumped into the air every year — greater than the local weather affect of transport and aviation mixed. Producing iron at lukewarm temperatures and with out coal would skip essentially the most emissions-heavy step with out counting on costly applied sciences.
That’s why Nijhawan’s concept caught Danielson’s consideration: Affordable inexperienced metal is a giant deal, and will disrupt an trade that generates greater than $870 billion in revenues every year. With the inexperienced mild to go forward and $2.25 million from BEV and different traders, Nijhawan began Electra — in stealth mode — to just do that.
Putting electrons to work
Stereotypically for a startup, Electra started its experiments in a storage. Nijhawan’s former colleague Quoc Pham joined as chief know-how officer. His first job was to work out whether or not it’s potential to dissolve iron ore in water laced with acid.
Failure got here inside weeks. “I have bad news for you,” Pham advised Nijhawan. “This could be the shortest startup of my life.”
To perceive what went unsuitable, let’s have a look at the three identified methods in which you’ll reduce emissions from steelmaking.
First, seize emissions generated by the method and bury them deep underground. The first such plant was inbuilt 2016 within the United Arab Emirates, however thanks to the upfront expense of carbon-capture know-how, none have been constructed since.
Second, use hydrogen as a substitute for coal. The first cargo of metal made utilizing hydrogen was produced final yr, however business volumes received’t be accessible till 2026. And since hydrogen made out of renewable electrical energy remains to be dearer than coal, firms are compelled to use high-grade iron ore, which there isn’t that a lot of.
“The world is running out of high-grade ores that are available for steelmaking,” says Nijhawan.
Third, use electrical energy. Metals like aluminium, copper and zinc are made utilizing electrical energy — admittedly, in a lot smaller quantities than iron. Until electrical energy turned low cost, it wasn’t economical to take into consideration making use of it to iron manufacturing.
However, you can not move electrical energy by way of stable iron ore. One resolution is to soften it. That’s what Boston Metal Co., a startup based in 2012, has completed. For the previous 10 years, it’s been perfecting and scaling the know-how, which works by heating iron ore to 1 400°C utilizing sufficient electrical energy to energy 1000’s of houses, and concentrating it right into a metallic field not a lot larger than a dumpster.
Lab tools at Electra. Image: Chet Strange/Bloomberg
Concentrating that a lot electrical energy into such a small space has to be completed utilizing particular supplies. Boston Metal can obtain it utilizing carbon as an electrode — a chunk of kit that permits power to circulate by way of with out itself melting — however that too generates carbon dioxide, defeating the aim of utilizing inexperienced electrical energy. Boston Metal discovered an alternate materials made up of iron and chromium, however to date it solely works on a pilot scale.
Nijhawan didn’t need to soften something. Once you’ve a course of operating at molten-metal temperatures, it has to run 24 hours and 12 months. If it does cease, the ore solidifies and new vats want to be put in place, inflicting months of delay. So the method had to be “benign from a temperature perspective,” he says — nothing hotter than the temperature at which “coffee is brewed.” That would permit for simple begin and cease, and make it potential to depend on intermittent renewables. But making the method work at such a low temperature required Pham to dissolve iron ore in water laced with acid.
“My pitch to all [the investors] was: ‘Look, I don’t know if this can be done. I’ve thought through the problem and asked the experts. I think there’s a feasible path,” Nijhawan says. “All I need is less than 10 people and maybe a year or year and a half to run this thing to the ground.”
He didn’t have to wait that lengthy. Pham went again to the drafting board, learn scientific literature and consulted specialists, together with Dan Steingart, professor of chemical metallurgy at Columbia University. After weeks of attempting new experiments, he discovered a profitable workaround.
Electra is now exiting stealth mode, and it refuses to publicly disclose its actual course of. However, Nijhawan and Pham shared sufficient particulars for impartial specialists to affirm that what the corporate claims to do is technologically possible.
“Electra has managed to pull off a difficult conversion going from iron oxide to iron using only electricity at such low temperatures,” says Venkat Viswanathan, affiliate professor at Carnegie Mellon University. “The steps they take trick iron to be in just the right state.”
A tour of the corporate’s Colorado facility additionally highlights its progress. There’s no coal-fired furnace or molten metallic, and lab demonstrations present how iron ore could possibly be dissolved. After {the electrical} course of is run, Electra produces plates the dimensions of workplace paper with a thick layer of iron metallic on them — silvery gray in look and surprisingly heavy.
The success of these experiments has helped Electra increase $85 million in complete from BEV, mining large BHP Group, Singapore-based fund Temasek Holdings, Amazon Inc. and some different traders. Now it simply has to scale up the know-how.
Iron age, continued
Electra is promising to construct a facility subsequent yr that can have a number of commercial-sized iron plates; just a few years after that, it plans to make 1000’s of plates in a bigger manufacturing facility. With Swedish metal large SSAB aiming to make business quantities of carbon-free metal by 2026 and Boston Metal promising to produce emissions-free iron by 2026, the race is formally on.
A full-sized business Electra plant can be a lot smaller than typical metal crops, which may generate 2 million metric tons of metal per yr, price greater than $1 billion, and are so massive that total cities spring up round them. Electra will look to construct crops that make solely 300,000 tons of metal every year, a dimension that would permit the startup to place itself close to present electrical arc furnaces. These furnaces take scrap metal and recycle it, and may use the iron Electra produces and tweak the method to make add extra virgin iron than scrap metal.
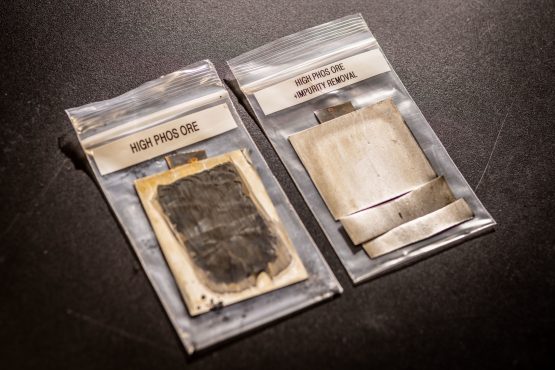
Examples of iron plates created utilizing iron ore with or with out impurities at Electra. Photographer: Chet Strange/Bloomberg
Another benefit could possibly be putting Electra crops shut to iron ore mines, that are sometimes situated far-off from city centres and close to land the place renewable energy will be constructed. Electra crops may then course of ore into iron on website whereas eliminating all impurities, drastically lowering the quantity of fabric that wants to be transported to a metal plant and additional reducing prices.
It may even be Electra’s first business software. In developing with a course of to dissolve iron ore, the corporate has additionally managed to take away impurities far more simply than typical steelmaking: At decrease temperatures, the impurities don’t chemically react as they’d in a furnace at 1600°C. The world is sitting on billions of tons of low-grade iron ore. It is likely to be potential for Electra to construct factories shut to these mines, and make present operations economically viable.
“Do or die in a startup is real,” says Nijhawan. “You don’t have 10 years to develop new science. You have to be in that pressure cooker, to be honest with you, rather than having infinite time available and resources available to see what can be done in a different way.”
© 2022 Bloomberg